Durch den Einsatz der Enterprise-AR-Software von LightGuide zur Standardisierung und Optimierung von Anweisungen mittels visuell geführter Workflows konnte ein globales Fertigungskonglomerat die Fehlerquote in Hydraulikschlauchsystemen von 769 fehlerhaften Teilen pro Million auf null senken und OEMs Millionen an FTC-Berechnungen für die Endmontage ersparen. Zusätzlich zu Qualitätssteigerungen erreichte das Unternehmen auch Verbesserungen bei Umrüstzeit und Schulungseffizienz.
- 769 fehlerhafte Teile pro Million vorher
- 0 fehlerhafte Teile pro Million danach
- 10 Minuten Umrüstzeit eingespart
Die Herausforderung
Angesichts tausender Teilevarianten ist Standardisierung entscheidend, um die Abläufe zu straffen und die Qualität zu sichern. Bei diesem Unternehmen führten 5.000 Varianten zu extremer Kundenspezifizierung, die die Mitarbeiter bei der Klebebandanbringung verwirrte. Die Schwierigkeit, für jede Variante die richtige Klebebandposition zu finden, führte im Lauf eines Jahres zu fast einem Dutzend Fehlern und zu Verlusten in Höhe von Tausenden von Dollar.
Diese Verwirrung entstand durch einen systemzentrierten Ansatz bei der Montage statt durch eine auf Aufgaben fokussierte Vorgehensweise. Veraltete Arbeitsanweisungen, die Kundenstücklisten gegenübergestellt wurden, waren uneinheitlich und führten zu fehlerhaften Montagen, die versandt wurden.
Gleichzeitig führte dieser systemzentrierte Ansatz zu langen Rüst- und Messzeiten für das Klebeband. Die Mitarbeiter waren unzufrieden, da ihre Arbeit wenig ansprechend war, viel Zeit in Anspruch nahm und häufig zu Fehlern führte. Statt strategischer Projekte lag der Fokus der Mitarbeiter auf der Behebung mechanischer Probleme.
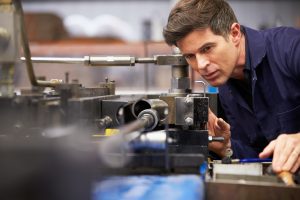
Die Lösung
Um die Produktion von 5.000 Teilevarianten zu rationalisieren, führte das Werksmanagement LightGuides Enterprise-AR-Software ein, mit dem Ziel, kontinuierliche Verbesserungen der bestehenden Prozesse zu ermöglichen, die Umrüstzeiten zu verkürzen und eine korrekte Klebebandplatzierung für höhere Qualität sicherzustellen.
Durch die Einführung projizierter AR-Software rüstete das Unternehmen die Mitarbeiter mit intuitiven visuellen Workflows aus und erstellte standardisierte Arbeitsanweisungen, um die enorme Zahl an Teilevarianten zu vereinfachen. So konnten die Mitarbeiter komplexe Fähigkeiten souverän beherrschen.
Dank der Flexibilität der Software konnten Bediener schnell zwischen Programmen wechseln, indem sie Barcodes, Seriennummern und andere Identifikatoren nutzten, um in Sekundenschnelle neue Montageschritte einzuleiten. Dadurch sanken die Umrüstzeiten stark, sodass insgesamt mehr Produktionszeit im Tagesverlauf verfügbar wurde.
Außerdem konnten die Mitarbeiter sicherstellen, dass sie am richtigen Teil arbeiteten, indem sie das Teil mit den eingeblendeten Abbildungen abglichen. So entfiel das Durchblättern von Arbeitsanweisungen, um das korrekte Teil zu finden.
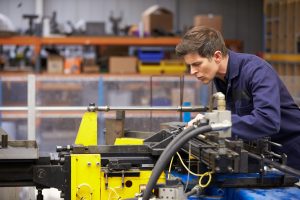
Die Ergebnisse
Mithilfe der Enterprise-AR-Software von LightGuide reduzierte das Unternehmen 769 fehlerhafte Teile pro Million auf NULL. Dies verbesserte die Kundenbeziehungen und erhöhte den fehlerfreien Prozessdurchsatz. Insgesamt führte dies zu keinerlei Kundenrücksendungen und bewahrte das Unternehmen vor Umsatzausfällen.
Das Unternehmen reduzierte außerdem seine Schulungskosten, da das System Teammitglieder in einer realen Arbeitsumgebung bereichsübergreifend schulen kann und sich dadurch gezielt auf relevante Fähigkeiten wie das Anpassen an kommende Varianten konzentriert wird.
Darüber hinaus haben die „Best-in-Class“-Schulungen und -Anleitungen die Umrüstzeit um 10 Minuten verkürzt, wodurch pro Tag eine zusätzliche Stunde Produktionszeit geschaffen wurde.