LightGuide + Lightning eMotors EV Wire Harness Routing

50%Decrease in Cycle Time |
75%Reduction in Training Time |
Introduction
Lightning eMotors is one of the leading companies revolutionizing EV manufacturing and fleet electrification. The company designs, engineers, customizes, and manufactures zero-emission-vehicle (ZEV) solutions for medium-duty government and commercial fleets. From delivery trucks and shuttle buses to passenger vans and more, it converts legacy combustion engine vehicles into battery-powered vehicles of the future.
To further its commitment to innovation and meet rising customer demand, Lightning eMotors expanded its manufacturing facility in 2021 and invested in new plant equipment to double its production capacity. As part of the expansion, the company integrated advanced manufacturing and automation technologies, including LightGuide’s projected augmented reality (AR) workflow platform, across multiple workstations and assembly areas throughout the plant.
Following the integration of LightGuide, Lightning eMotors optimized training and assembly workflows for breakthroughs in quality, productivity, and operational agility, enabling the company to adapt to demand more efficiently. Cycle time decreased up to 50% of the original build times and training time was reduced 75%. As a result of these improvements, Lightning eMotors also benefitted from cost savings, safety improvements, and decreased worker stress.
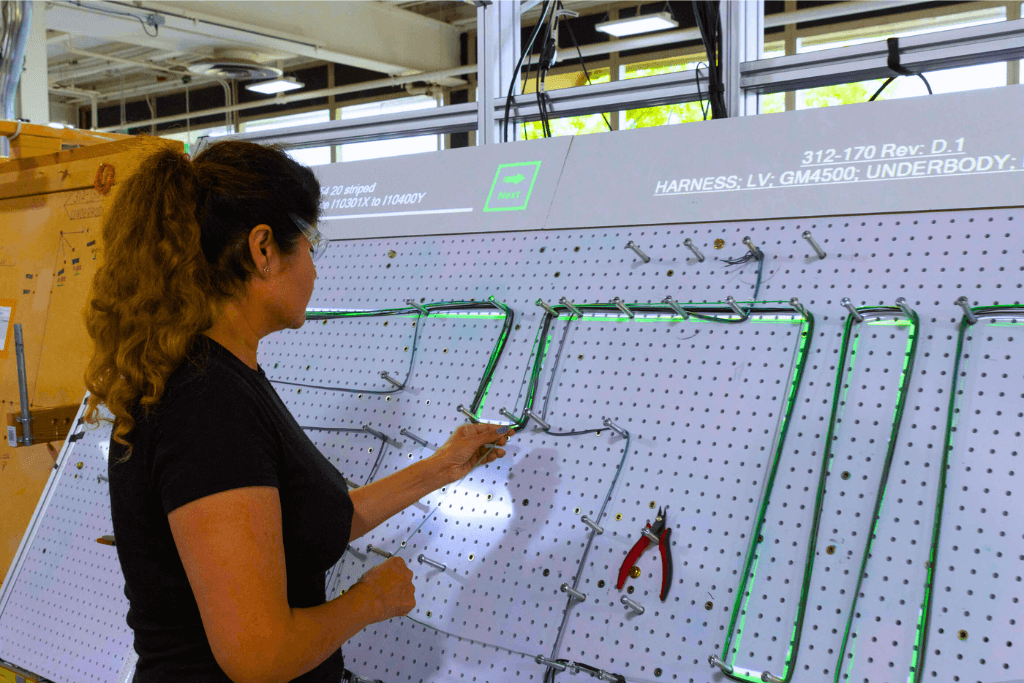
The Challenge
As the auto industry undergoes transformations to expedite EV production, manufacturers are challenged with the task of adapting workflows and training workers on new standards for safely producing EV components. To stay competitive in the market and scale production to meet demand, Lightning eMotors identified opportunities to further optimize high-variation, complex workflows for increased quality, efficiency and agility.
As Lightning eMotors searched for solutions that could enhance its operations, the team quickly realized the need for a comprehensive and versatile solution capable of facilitating multiple factory processes, such as picking, handling, assembly and training. After working with LightGuide channel partner DSI Innovations, Lightning eMotors discovered LightGuide’s projected AR workflow platform and immediately saw the benefit of using AR work instructions for a wide range of applications.
The Solution
Lightning eMotors immediately recognized the advantage of using LightGuide’s projected AR work instructions to standardize and streamline three assembly processes: their DC fast charge module, their high voltage power distribution unit (PDU), and a wide range of low voltage wire harnesses. By converting work instructions into a series of visual prompts projected directly onto workstations, the company effectively guided operators through intricate assembly workflows for wire harnesses and other critical components in real time. In addition, a second screen at some workstations shows photographs, diagrams, or video clips that clarify certain assembly steps. This approach not only facilitated process standardization but also yielded significant improvements in error rates, cycle times, and operator and end-user safety.
“It puts work instructions exactly where you build your product,” said Brandon Taylor, a Senior Process and Manufacturing Engineer at Lightning eMotors. “So you’re reducing time spent looking at printed instructions and other wasted effort, by putting the focus exactly where operators’ attention should be.”
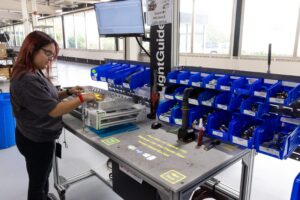
Testimonials
"[LightGuide] puts work instructions exactly where you build your product, so you’re reducing time looking at printed instructions by putting the focus exactly where operators’ attention should be."
With a workforce comprised of operators with diverse backgrounds and varying levels of EV manufacturing and component assembly experience, LightGuide played a pivotal role in helping Lightning eMotors bridge the experience gap. By standardizing workflows and providing comprehensive guidance, LightGuide empowered every operator to perform at their best and achieve optimal levels of quality and productivity.
The ability to simplify complex processes into a series of easy-to-follow steps eliminated the need for workers to memorize the entire procedure. Using a “no faults forward” approach, LightGuide also ensured each step in the process was completed correctly before allowing operators to advance to the next task. An example of this is the selection of wires for harness assembly. When it’s time to switch to a different color wire, the LightGuide system requires the technician to scan the barcode on the wire spool to confirm that the correct color of wire has been selected. As a result, operators experienced increased focus, reduced stress levels, and more pleasure in their work, allowing them to complete tasks with greater accuracy and efficiency.
To enhance employees’ comfort and confidence with complex manufacturing processes, Lightning eMotors took proactive steps to transition employees to LightGuide workcells. As part of this process, Lightning eMotors was able to provide one of its less experienced operators with additional support. This employee had a background outside of manufacturing and was worried about making errors that could compromise safety. Recognizing that a thorough, guided process would be key to empowering this employee, management swiftly relocated them to a LightGuide workcell. LightGuide’s comprehensive guidance not only alleviated the employee’s worries about making errors but also instilled a sense of confidence and pride in their abilities as a valued contributor to the team.
With more time spent focusing on the task at hand and less time trying to recall processes from memory, cycle times and production capacity also improved as operators incorporated lean ideals into their workflow. This increased focus also reduced the risk of safety hazards and defects during assembly, resulting in a safer product for end-users. This is especially important where the high-voltage assemblies are concerned.
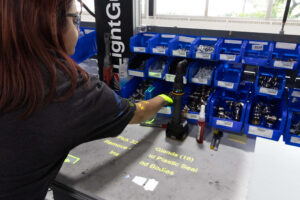
Accelerated Deployment of Work Instructions
With the large number of different wiring harnesses in Lightning’s products, it was especially important to be able to efficiently generate work instructions for each new harness, or if changes were made to an existing harness design. Taylor worked with LightGuide’s technical experts to develop a software tool which takes a spreadsheet and instantly converts it to the set of projected instructions needed to build a harness, complete with lines showing where each wire should be routed on the board.
“Previously, we would spend as many as three days designing and building custom layout boards for harnesses,” said Taylor. “Now, all I need to do is to add coordinates to a spreadsheet of wire definitions that I receive from our engineering team, and the software tool from LightGuide takes care of the rest in a few seconds. What’s more, I can work on the coordinate information at my desk, which means that I’m not tying up a valuable LightGuide station while developing the instructions.”
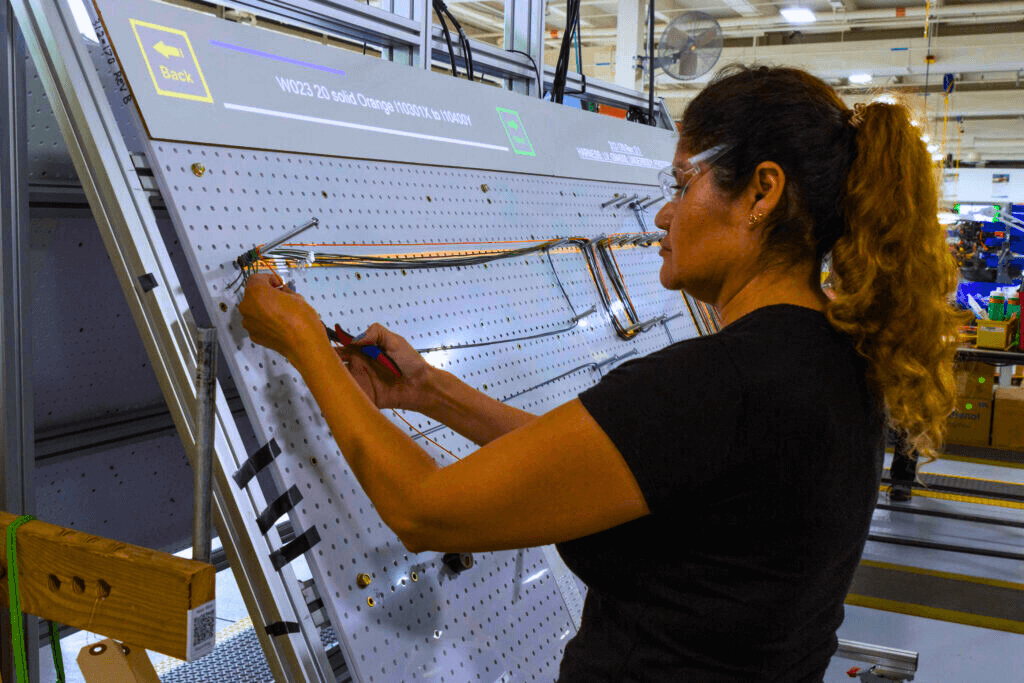
Improved Training Effectiveness
Due to the rapid innovation of EV manufacturing processes and the varying levels of employee experience, training processes can be complex and time-consuming. In addition to eliminating defects and ensuring safety, Lightning eMotors’ training program aims to condense the learning curve associated with mastering complex manual tasks.
Realizing the potential of AR to deliver interactive training experiences that simulate production processes, Lighting eMotors also began using LightGuide’s projected AR software to enhance the effectiveness of its training programs. As a result, workers were able to be placed on workcells faster, and with less oversight, as the technology provided comprehensive guidance and increased workers’ confidence in their ability to safely and successfully complete tasks.
Testimonials
"LightGuide really helps people who haven’t done this before and helps them integrate into the process."
“LightGuide really helps people who haven’t done this before and helps them integrate into the process,” said Brandon Taylor.
Once projected AR was integrated within training programs, Lightning eMotors improved traditional and cross-training methods while reducing training time from a half day to about an hour. This allowed the company to allocate more resources toward identifying other opportunities to improve organizational strategy.
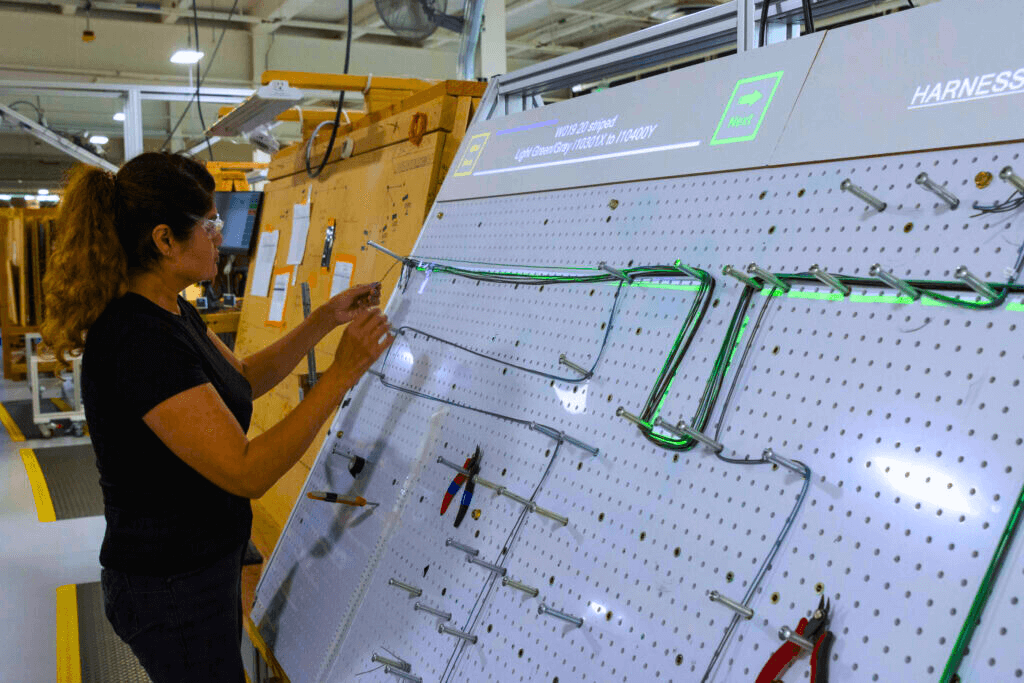
The Results
- A reduction in cycle time up to 50% less than the original build times
- Condensed training time by 75% to about an hour, while improving overall training effectiveness
- Guided workflows resulted in safety improvements and decreased worker stress
- Increase in efficiency and production capacity, as well as cost savings in unnecessary rework and lost productivity caused by defects
“These systems give us a level of sophistication that impresses our customers,” concluded Taylor. “It gives us confidence in what we do.”
Testimonials
"[LightGuide] systems give us a level of sophistication that impresses our customers. It gives us confidence in what we do."
Through harnessing the capabilities of LightGuide’s projected augmented reality (AR) platform, Lightning eMotors achieved a significant boost in overall efficiency, ensuring the refinement of their manufacturing and training processes. This strategic implementation not only upheld their commitment to high quality and safety standards but also propelled their competitiveness within the electric vehicle (EV) industry.
Related Content: 3 Uses of Augmented Reality in Automotive Manufacturing