A Complete Guide to Augmented Reality for Medical Manufacturing
If you’re in medical manufacturing, you have the privilege of helping save and improve the lives of patients through innovative products. But the privilege comes with high responsibility. The slightest error can have dire consequences, and medical manufacturers need comprehensive solutions to prevent product defects—solutions that are as innovative as the products they make.
Augmented reality (AR) in medical manufacturing is a new way to bring discipline to production processes with a no-fault forward approach to manual assembly. Augmented reality provides a variety of operational improvements, from standardizing processes, providing intuitive and interactive work instructions, capturing rich data that can help improve quality, and providing invaluable Together, these improvements transform medical manufacturing, addressing and solving every challenge manufacturers face.
3 Challenges Medical Manufacturers Face
Maintaining Consistent Quality
One of the biggest challenges in medical manufacturing is ensuring that production processes yield consistent quality. Quality issues in production can be an obstacle to operations, increasing cycle time and reducing throughput. If a defective product is released into the market, there can be serious consequences for both patients and manufacturers.
As healthcare products become more intricate and complex, the ability to ensure quality becomes more challenging. Manufacturers need a way to manage the risk of inconsistency and human error in assembly. By analyzing the data from AR-enabled processes, medical manufacturers can identify sources of quality problems early and streamline manual tasks to ensure that each assembly meets standards.
Ensuring Patient and Operator Safety
Inconsistent quality and a lack of standardization across manual processes can risk the safety of end-users, leading to serious consequences for consumers and medical manufacturers. To reduce errors and avoid liability and damage to the company’s reputation, manufacturers need a fool-proof method to ensure every product leaving the factory conforms to internal and regulatory standards. The best way to achieve this is by standardizing work instructions and validating the use of PPE in processes that require it.
In addition to end-user safety, every process needs to ensure operator safety. Complex manual processes can frustrate operators, who may be motivated to “simplify” a step with an unsafe workaround. But on the factory floor, it can lead to injury, disruption, and the possibility of liability.
Acknowledging and Addressing Liability
Of course, medical manufacturers aren’t responsible for every product defect and it’s not always obvious what went wrong. Damage in shipping can cause problems and the end-user may not use the product as directed. Both can lead to lengthy liability cases, affecting customer perception and business relationships.
When faced with a product liability lawsuit, manufacturers are challenged to determine responsibility. The ability to conclusively determine that a defect was caused by a third party after manufacturing will help reduce liability claims. If a defect was caused in manufacturing, the ability to recreate the actual source of the defect is invaluable for correcting mistakes in the future.
In an industry where the stakes are high and quality is critical, medical manufacturers and engineers must be confident their products are developed the same way every day, every shift, every time.
To get a better idea of how AR solves these problems, we’ll take a look at three use cases of AR for medical manufacturing that can be applied to your operations.
RELATED ARTICLE: What Does Augmented Reality Have to do with ALCOA+ Data Standards?
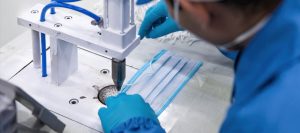
3 Applications of Augmented Reality for Medical Manufacturing
Augmented reality helps ensure quality by putting the right information in the right place at the right time for every manual process. AR enables medical manufacturers to reduce errors and exposure to liability through the ability to deliver consistent high-quality results.
Using advanced projection technology, LightGuide’s enterprise AR software overlays a virtual operating “canvas” onto any work surface and guides operators through each step of a process through a series of visual and audio prompts.
There are several applications for AR in medical manufacturing, each of which contributes to quality and consistency across processes, people, and factory locations.
Standardization of Work Instructions
Consistent precision is essential for optimal results. But with different people working different shifts—or even in different locations—enterprise process standardization can be varied.
AR gives medical manufacturers the ability to write and deliver standardized work instructions that are intuitive, interactive, and easy to follow. As a result, medical manufacturers can be confident that each product is built the same way, every time, every shift—regardless of whether the product is a pacemaker, prosthetic, or pharmaceutical.
This consistency leads to improved quality, especially if AR software is programmed to support a no-faults forward approach to medical manufacturing. With improved quality and consistency, manufacturers can reduce their exposure to liability while delivering better outcomes for end-users of the products being developed.
RELATED ARTICLE: 3 Ways AR Makes It Easier to Write Work Instructions
No-Fault Forward Instructions Ensure Quality
By verifying each step of the process as it’s performed, augmented reality ensures a “no-fault forward” approach to manufacturing. Operators can’t move on to the next step or assembly until the current step is completed correctly and in the appropriate manner. This virtually eliminates the human error associated with manual processes and ensures consistent quality because the right parts, processes, and sequences are always used.
Enhanced Product Traceability
Data collected through augmented reality gives manufacturers improved traceability—the ability to take a deeper look into manual processes in order to improve quality and gain control over how tasks are carried out. Traceability gives manufacturers a broader view of an entire production process, making it easy to pinpoint areas for improvement, identify bottlenecks, and detect processes causing defects.
The ability to retrace steps is also crucial for addressing liability concerns. LightGuideAR software creates a “digital birth certificate” of each individual part’s serial number and tracks it throughout the entire manufacturing process.
This is a huge benefit for liability cases where a product defect doesn’t originate with the manufacturer. The proof is in the data collected by LightGuide’s AR software throughout the manufacturing process. In cases where a defect does originate in manufacturing, companies can use the saved process data to identify the source of the defect with pinpoint accuracy.
RELATED ARTICLE: The Power of Product Traceability in Manufacturing
Manage the Complexity of Medical Manufacturing with Confidence
Medical products are getting more complex, and that complexity is mirrored in manufacturing processes. AR solutions designed to alleviate the challenges of modern manufacturing can help medical manufacturers standardize processes, improve quality and ensure safety. With fewer quality and liability concerns, manufacturers can improve ROI and build their company’s reputation.
Interested in learning how LightGuide’s AR software can improve your medical manufacturing processes? Contact us to schedule a consultation with one of our AR experts.