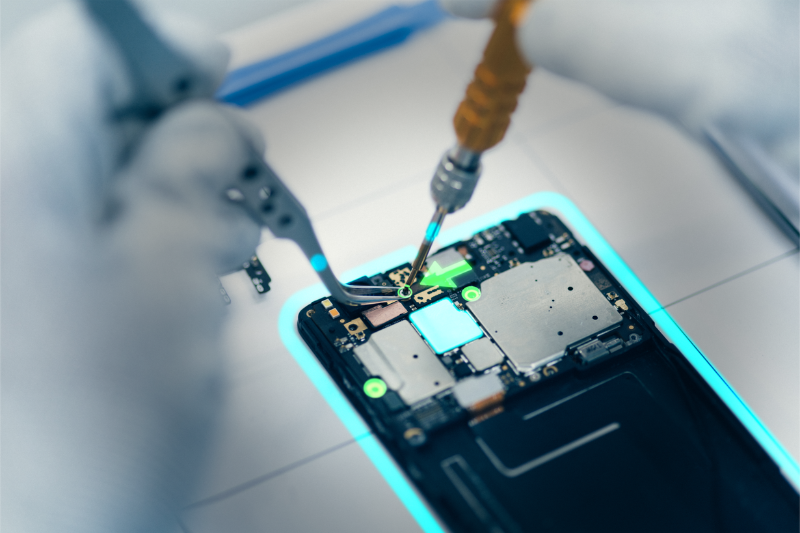
Electronics manufacturing is a fast-paced world. The luxury of having months to gear up for a new product run is long gone and manufacturing processes must be designed to deliver the next generation of smart devices and data center infrastructure in an accelerated timeframe.
On top of that, products are becoming more complex, the skills gap is getting wider, and manufacturers are challenged with increasing production and improving quality to meet growing demand – all while navigating component shortages and scaling up e-waste recycling programs.
This places a huge burden on electronics manufacturers to update work instructions faster than ever and train employees on their many variations. To get ahead of these challenges, electronics manufacturers are using augmented reality (AR) to:
- Streamline the deployment of standardized work instructions
- Improve training effectiveness
- Standardize assembly processes for enhanced quality control
- Reduce repair complexity
- Optimize electronics recycling processes
The Current State of Electronics Manufacturing + 5 Challenges AR Can Solve
- Updating Work Instructions to Support New Product Launches
- High Employee Turnover & Inadequate Training
- Quality Control
- Managing Repair Complexity
- Reducing E-Waste and Creating a Sustainable Supply Chain
Challenge #1: Updating Work Instructions to Support New Product Launches
Shifting consumer preferences force electronics companies to introduce new products at a faster pace than ever before. Shorter product lifecycles, coupled with increasingly higher levels of innovation, are leading to an explosion in the sheer number of products and their variations. For example, iPhones are highly customized with different capacities, capabilities, and colors, which add complex variations to electronics manufacturing processes.
To meet production quotas (and maintain quality standards), electronics manufacturers must update standard operating procedures, develop new work instructions, and train workers on new products and variations.
Traditionally, work instructions have been deployed as instruction manuals or displayed on computer screens. Not only are these difficult to update at scale, they’re ineffective. When employees are constantly looking at manuals and monitors, they’re distracted from their work, leading to inefficiencies such as longer cycle times, increased opportunities for error, and ultimately, lower yields.
How AR Standardizes, Streamlines & Error-Proofs Work Instructions
Many electronics manufacturers have multiple factories and locations that must be brought up to speed with each new product launch. As new designs are released into production, the best augmented reality solutions enable electronics manufacturers to update work instructions across manufacturing facilities, ensuring consistency by giving every employee in every location the same set of instructions to work from.
AR also transforms text instructions into visual cues that can be projected onto any work surface. This enables manufacturers to distill pages of complex work instructions into visual step-by-step instructions that are easy to understand and follow. With work instructions visualized on a work surface, assembly instructions are much easier and faster to comprehend when compared to reading instructions from a screen or sheet of paper.
RELATED ARTICLES:
- 3 Ways AR Makes It Easier to Write Work Instructions
- Digital Work Instructions Explained: The Ultimate Guide
- 6 Tips for Writing Practical Work Instructions
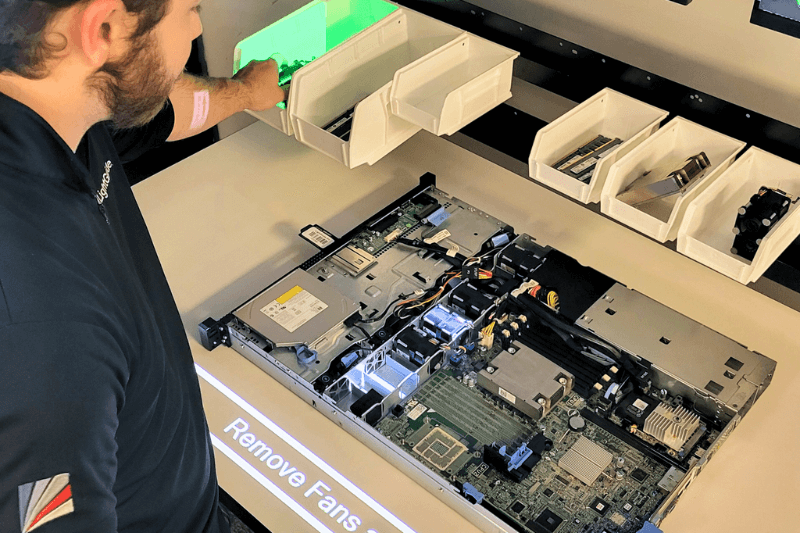
Challenge #2: High Employee Turnover & Inadequate Training
Employee turnover is keeping electronics manufacturing companies at a chronically low level of productivity. Often, workers are trained through tribal knowledge that is passed down by more experienced personnel. This method always leaves gaps. And as older workers retire, tribal knowledge will be more difficult to rely on.
The need to continuously retrain workers is making it difficult for electronics manufacturers to maintain quality standards. To stay competitive, electronics manufacturers must find a way to deliver comprehensive training and guidance in a way that encourages employees to stay at their job for the long term. The training must also be efficient and fast enough to keep pace with product changes.
How AR Improves Training
Low-tech, “old school” methods of training are not keeping up with the high-tech needs of electronics manufacturers. By projecting work instructions directly onto any work surface, AR simplifies complex manual processes and makes it easier and faster to train, upskill, and cross-train employees. This reduces the ramp-up time for new and reassigned employees and empowers them to hit their productivity and quality goals from day one.
- Interactive simulations: AR training modules replicate real-world scenarios, allowing employees to gain on-the-job experience in a controlled environment. This hands-on experience boosts engagement and retention, helping employees grasp concepts more effectively.
- Real-time guidance and feedback: As workers are learning a new task, AR can be used to provide trainees with instant feedback. This helps trainees identify and correct errors on the spot, accelerating the learning curve and reducing the time it takes to learn new skills.
- Personalized training: Customized training modules can be tailored to meet specific skill development needs, whether it’s assembling a new product, mastering quality, or learning safety protocols.
RELATED ARTICLE: How to Use Augmented Reality to Upskill Workers
Challenge #3: Quality Control
Because electronics companies outsource much of their manufacturing, contracted manufacturers, repair companies, and recycling facilities are under pressure to deliver extremely low margins of error as a condition to keep their contracts. When processes and work instructions aren’t standardized for each product and variation, it’s difficult to ensure consistent quality across manufacturing facilities. In addition, high turnover naturally leads to quality issues without a foolproof training process and clear, step-by-step instructions for each assembly, repair, or recycling process.
How AR Improves Quality Control
LightGuide’s projected AR software transforms manual processes by superimposing digital step-by-step work instructions onto an employee’s work surface, standardizing and error-proofing the work. Coupled with 3D sensors and vision cameras, the system prevents and detects errors in real time while capturing data and insights on operator performance and quality.
This no-fault forward approach ensures each step is completed correctly before allowing the worker to move to the next task and builds quality into manufacturing processes, leading to higher yields and the added benefit of decreased cycle times.
From the moment an employee starts their shift to the point where an assembly or repair is completed, LightGuide’s AR platform enables electronics manufacturers to capture real-time operational metrics for full digital traceability into a product’s production history. This level of visibility into manual processes and operations can be used to identify areas for improvement that can lead to higher efficiency, while quality issues can be easily pinpointed and addressed. The ability to optimize processes can also help contracted partners make a strong case to their OEM partners that they can consistently meet specifications.
RELATED ARTICLE: The Power of Product Traceability in Manufacturing
Challenge #4: Managing Complex Repairs
As technology advances and our dependence on digital devices grows, so does the need for reliable electronics repair services. As new devices are released, electronics repair companies face the formidable challenge of adjusting operations to accommodate a diverse range of device types, all while maintaining safety, speed, and customer satisfaction. This includes equipping technicians with proper tools and training and updating processes in alignment with Right to Repair laws, which advocate for greater accessibility and transparency in the electronics repair process.
Devices like smartphones, tablets, computers, gaming consoles, servers, and appliances require specialized repair procedures. The high degree of variation among these devices, and the lack of standardization, make it difficult for repair companies to create effective work instructions, as each device may have unique hardware components and configuration requirements.
How AR Reduces Repair Complexity
To address these challenges, companies are turning to Industry 4.0 technologies, like AR, to facilitate faster, safer, and more reliable repair services. Some benefits of AR for electronics repair include the ability to:
- Standardize repair processes and reduce complexity by transforming instructions into visual workflows that guide technicians in real time
- Prevent errors and improve bounce with integrated sensors and vision cameras that confirm repairs are completed correctly
- Create effective training programs that reduce the learning curve for new hires and increase proficiency on devices with low repair volumes or higher bounce rates
- Improve traceability and gain insight into valuable repair data, with the ability to track throughput, mean time to repair, and bounce rates by device type
RELATED ARTICLE: The Future of Electronics Repair: How AR is Transforming Tech Support
Challenge #5: Reducing E-Waste and Creating a Sustainable Supply Chain
The electronics industry is also under increasing pressure to reduce its carbon footprint. As consumers demand more eco-friendly products and governments introduce regulations that emphasize sustainability, electronics manufacturers are faced with the challenge of balancing demand for new products and business performance with the need to reduce their environmental impact. As a result, electronics recycling has become a key area of focus for many manufacturers.
According to Dell Technologies, 53.6 million tons of electronics become e-waste each year, making it the fastest growing waste stream. The rapid pace of technological advancement and short lifespan of electronic devices are contributing to this growing problem. However, amid this challenge lies an opportunity. Discarded electronic products offer a readily available source of valuable components and rare earth metals that can be recycled and used to manufacture new electronic devices.
How AR Enhances Recycling Processes
Using these recycled materials to produce new electronic devices is a strategic way to conserve resources, strengthen supply chain resilience, foster innovation, and drive business growth. However, the path to creating a more sustainable electronics manufacturing ecosystem is not without its challenges. Fortunately, advanced manufacturing technologies, like AR, are making it easier for companies to safely recycle, recover, and reuse materials from discarded electronic devices by:
- Simplifying the process of disassembling devices and sorting diverse waste streams by superimposing real-time guidance onto work surfaces
- Building quality into recycling processes and increasing recovery margins, preventing contamination, and creating a sustainable closed-loop supply chain
- Highlighting potential hazards to reduce safety risks
- Enhancing traceability for deeper insights into material recovery initiatives
RELATED ARTICLE: Electronics Recycling & E-Waste Management: A Technological Revolution is Underway
Manage the Challenges of Electronics Manufacturing with Confidence
The electronics industry is booming. That means the flood of new products will continue and the need to train and retain workers will become more crucial to success.
Augmented reality from LightGuide can help electronics manufacturers gain a competitive edge by improving training, standardizing work instructions, and ensuring error-free manufacturing with no-fault forward processes. Traceability provides the added benefit of data that can be used to improve processes for peak efficiency and quality.
In combination, the benefits of AR for electronics manufacturing can help your company win more contracts and become the go-to supplier for quality and volume.
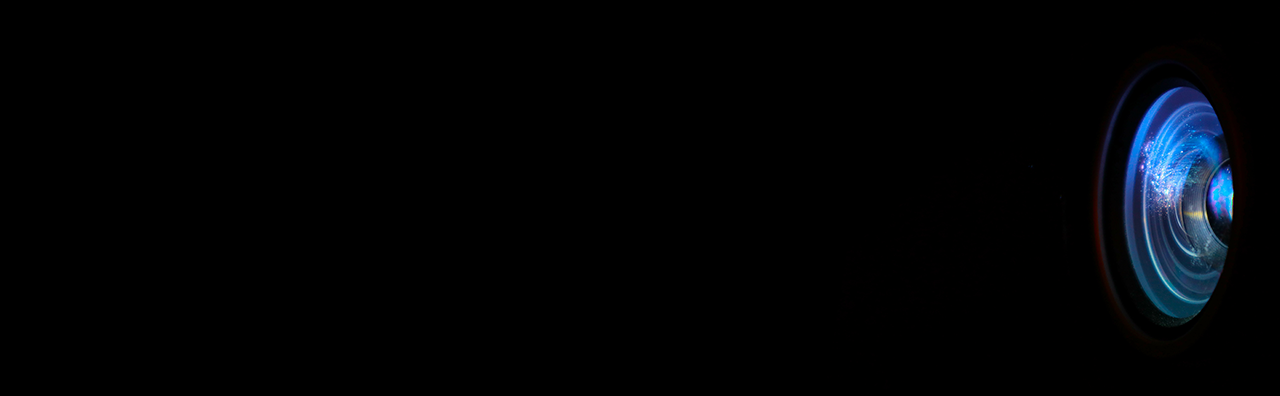
Interested in learning how AR can improve your electronics manufacturing processes?
Contact us to schedule a consultation with one of our AR experts.