As technology advances and our dependence on digital devices grows, so does the need for reliable electronics repair services. Devices are becoming more complex, making them difficult to repair and costly to replace — posing challenges for both consumers and companies that manage electronics warranty support and repair claims.
As new devices are released, electronics repair companies are faced with the formidable challenge of adjusting operations to accommodate a diverse range of device types, all while maintaining safety, speed, and customer satisfaction. This includes equipping technicians with proper tools and training and updating processes in alignment with Right to Repair laws, which advocate for greater accessibility and transparency in the electronics repair process.
To overcome these operational hurdles and remain competitive in the fast-paced and constantly evolving electronics repair landscape, companies are exploring innovative new ways to use Industry 4.0 technologies, like augmented reality (AR), to facilitate faster, safer, and more reliable repair services.
The Current State of Electronics Repair + 4 Challenges That AR Can Solve
Hundreds of millions of electronic devices are repaired each year. Best Buy reported repairing more than 1.7 million devices in 2022, and Asurion, the owner of uBreakiFix, repairs 4.5 million devices every year.
The sheer magnitude of repairs alone can place significant pressure on any business, not to mention the arduous task of adapting processes to accommodate a growing variety of devices, ranging from smartphones and tablets to computers, gaming consoles, appliances, servers, and more.
This massive undertaking entails processing hundreds of repairs each day, many of which have unique requirements based on the type of device or component being repaired. These added layers of complexity can lead to inefficiencies and quality issues that expose gaps in the current process and challenges that need to be addressed.
Challenge #1: Ineffective Work Instructions for Complex & Varied Electronics Repairs
One of the biggest challenges electronics repair companies face is a high degree of variation and lack of standardization. Devices have grown in complexity, and new models are constantly being released. This can make it difficult for companies to update repair procedures, as each device may have its own unique hardware components and configuration requirements.
For example, repairing a smartphone screen may involve replacing the glass, the touch sensor, and the display. Whereas repairing a smart speaker may require fixing the microphone, the speaker, the power supply, and more.
To complicate matters further, many electronic devices contain miniature components that require pinpoint precision, leaving no room for error. Depending on the components or products being repaired, companies run the risk of significant errors arising from the oversight of even the smallest step in the process.
This means companies need to be extremely diligent when authoring repair instructions. They also need to come up with a dynamic solution that can be easily updated and is practical for employees to use.
The AR Solution: Digital Work Instructions That Reduce Electronics Repair Complexity
In the rapidly evolving consumer electronics industry, repair companies need an agile way to adapt their work instructions. Augmented reality standardizes complex electronics repair processes by overlaying visual work instructions onto the device or component being repaired.
The ability to display work instructions in a single, unified view eliminates the need for technicians to recall instructions from memory or switch between multiple sources of information. This can help to reduce the risk of missed steps and improve the time it takes to complete repairs.
Through a simple barcode can or program selection, technicians can quickly and easily access the right work instructions every time. Within a matter of milliseconds, workers can get started on a smartphone from a completely different brand and model than the cycle before, reducing downtime.
In addition to improving efficiency, AR work instructions can help improve repair quality. Using integrated sensors and vision cameras, LightGuide’s AR software is able to verify the correct completion of each task before allowing operators to move to the next step.
Finally, AR work instructions can help reduce the need for paper-based instructions. Paper-based instructions can be outdated, incomplete, or inaccurate. AR work instructions, on the other hand, are always up-to-date and can be customized to the specific device being repaired.
Watch how LightGuide AR work instructions can also streamline and error-proof rack server maintenance and refurbishment processes. With LightGuide, technicians receive precise, real-time guidance projected directly onto the server, streamlining complex processes and reducing errors.
RELATED ARTICLE: 3 Ways AR Makes It Easier to Write Work Instructions
Challenge #2: High Employee Turnover & Inadequate Training
While updating repair instructions is crucial, it’s only one part of the equation. Providing technicians with the proper training and skills to repair devices safely and efficiently is also key.
Electronics are complex systems and repairing them requires specialized technical knowledge. However, the industry’s rapid technological advancements and changing repair procedures make it difficult to keep training materials updated and create a steep learning curve for employees. Frustration among staff, stemming from inadequate training and difficulty keeping up with changing procedures, can lead to increased turnover rates.
To address these challenges, electronics repair companies must rethink their approach to workforce development and adopt effective training methods that reduce the ramp-up time for new employees and provide experienced technicians with ongoing opportunities to improve proficiency.
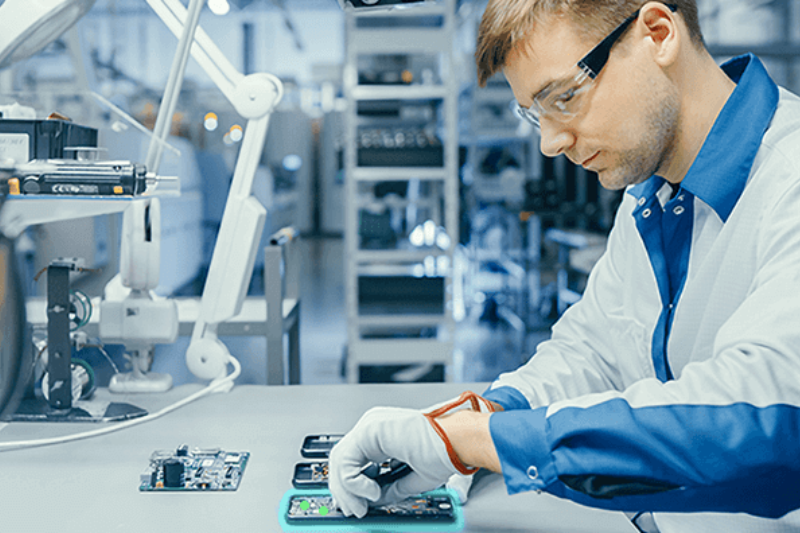
The AR Solution: Interactive Training That Enhances Operator Proficiency
Assistive AR technology reduces the learning curve for new hires and helps seasoned technicians stay updated on the latest technologies. Using projected AR workstations, companies can create training experiences that mirror real-world scenarios. This safe and controlled method of training allows employees to practice repairs exactly how they would on the line, without the risk of causing operational delays or errors.
LightGuide’s projected AR software also enables companies to track trainee progress and issue certifications once specific criteria have been met. This may include accurately completing a set number of cycles, passing a quiz, or demonstrating readiness through additional proficiency tests. Not only is this a useful tool for training new hires, it can also be used to certify technicians on new devices and increase proficiency on devices with low repair volumes or higher reship rates.
Embracing this approach allows companies to enhance the caliber of their training programs while offering technicians immediate feedback on their performance. By expediting employee proficiency and minimizing the onboarding time for new team members, companies can mitigate the challenges of employee turnover and gain an edge in retention and production quality.
Challenge #3: Poor Quality and Lack of Traceability
Customers want to be assured their devices are repaired by credible and qualified companies that can guarantee the quality of their work. However, achieving consistent repair quality across all devices remains an ongoing challenge.
Variations in technician expertise, coupled with the complexity of modern electronic devices, can lead to inconsistent repair outcomes. This variability not only affects customer satisfaction but can also increase the likelihood of costly rework, returns, and warranty claims.
Another big challenge is the lack of traceability. Traditional repair methods often lack the ability to capture essential process data, such as step times, cycle times, and images during the repair process. Without this valuable information, it becomes challenging for companies to ensure repairs meet internal quality standards. This lack of traceability also makes it difficult for companies to identify the source of problems when issues occur, which can lead to unnecessary repairs and waste of resources.
RELATED ARTICLE: The Power of Product Traceability in Manufacturing
The AR Solution: Enhanced Traceability & Quality Control for Complex Electronics Repair Processes
In addition to providing technicians with visual guidance, LightGuide’s projected AR technology can be used to capture valuable process data for increased traceability and enhanced quality control.
With inspection at every step, and the ability to capture operator IDs, cycle times, and photos as repairs are being performed, companies can generate a certificate of completion for each device by IMEI that contains a historical record of valuable repair data.
This enhanced traceability offers companies deeper insights into the proficiency of their technicians, allowing them to pinpoint where errors occur and identify areas for further process improvements.
Challenge #4: Safety Hazards Caused by Mishandling Devices
Electronics repair, while essential for keeping our devices running smoothly, is not without its risks. One of the most critical concerns in this field revolves around the safe handling of batteries and power supplies.
Lithium-ion batteries, commonly found in many electronic devices, are known for their energy density and power. However, they are also susceptible to a phenomenon called thermal runaway. This occurs when a battery overheats, potentially leading to fire or even explosion. Technicians who mishandle batteries, apply incorrect charging methods, or puncture them inadvertently increase this risk.
Batteries also contain chemicals that can be harmful when exposed to skin, eyes, or even inhaled. Mishandling a damaged battery can lead to leaks, potentially releasing toxic substances that can cause skin irritation, chemical burns, or respiratory issues. Improper disposal of damaged or leaking batteries can also harm the environment and cause chemicals to leach into the soil and water. Proper disposal and recycling procedures are crucial to mitigate these environmental risks.
The AR Solution: Real-time Guidance for Increased Safety
With optimized work instructions and training in place, workers are at reduced risk of mishandling components that could lead to safety issues. Using a no-faults-forward approach to repair, companies can ensure employees follow inspection and safety guidelines by preventing technicians from continuing a task if they have not waited for safety features to complete their cycles.
For example, during a smartphone disassembly workers may need to wait specific amounts of time for a heating tool to separate adhesives within a phone. By grabbing it too early, a worker risks burning themselves. If they wait too long, the adhesive may start to solidify again and make it difficult to open the phone, therefore risking damage by trying to pry the phone open.
Optimizing Electronics Repair Processes with Digital AR Workflows
The consumer electronics industry is constantly evolving, and so are the needs of consumers. Today’s consumers expect their devices to be repaired quickly, efficiently, and accurately. To meet these expectations and remain competitive in today’s electronics repair landscape, companies need to evolve their processes.
The rapid influx of new devices and the inherent complexity of electronic repair processes necessitate a shift toward digitization. As traditional electronics repair methods struggle to keep pace with the rapid and constant pace of change, advancements in projected augmented reality are opening the door to a new era of efficiency, speed, and quality in the electronics repair industry. With projected AR, companies can standardize intricate repair processes and improve training for enhanced quality and operational efficiency.
Ready to standardize your electronic repair operations? Get in touch with our team of AR experts to explore solutions to your biggest challenges.
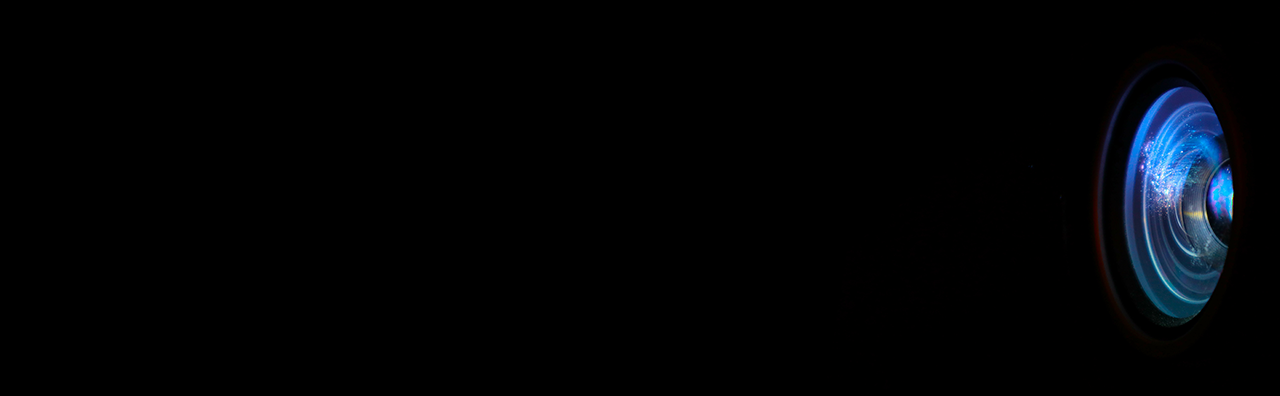
Ready to Transform Your Electronics Repair Processes?
Contact us today for a personalized demo of LightGuide’s AR solutions.