Model changeovers, interior and exterior facelifts, and new product launches keep automotive OEMs and suppliers on their toes. While automation and other technologies are helping manufacturers become more efficient, the pressure to innovate and adjust to change never ends.
Automotive manufacturers are expected to gear up for new products faster than ever, compressing the time it takes to adjust to change. And with electric vehicles (EVs) now part of the mix, complexity is increasing as manufacturers are challenged to manage even more product variations.
As automotive manufacturing becomes more complex, companies are challenged to maintain and improve quality while also increasing productivity. To maintain business, OEMs and automotive suppliers must respond to change quickly while ensuring products are manufactured with stable, repeatable processes.
Benefits of AR for Automotive Manufacturing
Never-ending production changes, paired with more complex standards, are causing manufacturers to reassess solutions for maintaining quality and efficiency. As such, companies are exploring the benefits of augmented reality (AR) for automotive manufacturing and finding that AR gives OEMs and suppliers a competitive edge by improving quality and throughput.
Let’s take a closer look at four automotive manufacturing challenges that augmented reality solves.
- Standardizing and Streamlining Manual Processes with High-Variation
- Optimizing Training
- Improving Quality Control
- Enhancing Traceability
- Real-World Use Cases and Success Stories
Challenge #1: The Struggle to Standardize Manual Processes
One of the biggest challenges facing automotive manufacturers is the ability to standardize manual processes, particularly those with high variation. For example, the Dodge Dakota has 48 different wire harnesses just for the headliner. It’s all too easy for processes like this to get bogged down in confusion, frustration, and rework.
Traditionally, operators follow work instructions from a sheet of paper or screen. In a high-variation environment, this can be distracting. Operators need to regularly reference the instructions as they work, which distracts their focus and erodes productivity. In many cases, instructions can be unclear to workers, forcing them to leaf through dusty binders to find answers to process questions. How productive is that?
In addition, creating work instructions is a tedious and time-consuming process that can be tough on engineers. And despite manufacturers’ best intentions, when processes change, work instructions often aren’t updated.
How AR Work Instructions Standardize and Streamline Complex Manual Processes
AR standardizes and streamlines complex procedures to reduce variability and increase production outcome consistency by distilling endless work instructions into an intuitive, easy-to-understand process. All operators need to do is bring their parts to the workstation, scan the barcode, and their AR work instructions are immediately retrieved so they can get right to work.
AR software from LightGuide guides operators through each step of a manual process with audio and visual prompts, pacing, and direction, so all they have to do is follow the lights. By projecting work instructions directly onto the work surface, operators no longer need to memorize each step and can quickly assimilate to new processes. This eliminates distractions and enables them to stay focused on the task at hand, leading to greater productivity and the ability to effortlessly handle tasks with higher levels of variation.
With standardized work instructions, employees making the same product at different workstations—or in separate locations—get the same instructions because AR puts the right information in the right place at the right time for every operator.
When instructions need to be changed, either to optimize a process or accommodate a new product or variation, the instructions can be updated once and published across the enterprise or shared with suppliers. This means work instructions written in the United States can be adapted to plants in other countries, fostering a consistent standardization of assembly processes across global operations.
Challenge #2: High Employee Turnover and Inefficient Training
Training programs are costly and challenging to manage, especially when training needs to be updated for new products and variations. Often, training is managed by multiple people—who all have their own style, tips, or tricks—which can result in inconsistencies. This can lead to inconsistency in production outcomes such as increased error rates, production time, and even safety hazards.
In addition, automotive OEMs and suppliers must deal with the ever-widening skills gap. As older workers retire and take their knowledge and experience with them, training new workers becomes a bigger challenge. In a high-tech production environment, automotive manufacturers need workers who are skilled, flexible, and can quickly adjust to change.
How AR Improves Training
Augmented reality training creates interactive and immersive training experiences that simulate real-world production processes, allowing new and reassigned workers to grasp complex concepts quickly. Because AR trains employees on best practices from the start, training becomes standardized and consistent and enables manufacturers to quickly train substitute workers when an employee is absent.
LightGuide enables manufacturers to easily create high-impact, immersive training programs by creating a virtual operating canvas that’s projected onto any part or assembly. Trainees are guided step-by-step through work instructions using visual and audio prompts. The system tracks trainee progress and uses data to issue certifications and provide personalized training based on areas for improvement.
Challenge #3: Quality Issues
The automotive industry thrives on precision and efficiency, and any disruptions in the production line can have significant downstream consequences. Errors in kitting, assembly, or inspection can lead to rework, production issues downstream, warranty claims, and other drains on productivity and profit. Even more critical are the potential safety hazards associated with faulty components, which can have life-threatening consequences.
Maintaining consistent quality control becomes increasingly challenging due to the complexity of modern vehicles, each with intricate systems and numerous components. Additionally, managing quality across global supply chains introduces complexities and increases the risk of inconsistencies.
Fortunately, advancements like LightGuide’s AR work instructions offer a solution. By providing clear, visual guidance, real-time feedback, and improved training, AR technology empowers manufacturers to build quality into the production process, ultimately enhancing efficiency, safety, and brand reputation.
How AR Work Instructions Improve Quality Control
From enhanced training and precision guidance to quality control, AR error-proofs core manufacturing operations, including kitting and sequencing, assembly, training, inspection, and more. The possibilities are endless. Let us show you how!
Eliminating Part Picking, Kitting & Sequencing Errors
One area ripe for improvement is the manual tasks associated with part picking, kitting, and sequencing. For example, it’s not uncommon for manufacturers to kit components to a build line. But kitting issues, such as incomplete kits or kits with the wrong parts, can bog down the production line. Using projected augmented reality technology from LightGuide, manufacturers can build quality into the kitting process by guiding workers to the correct part and confirming the picks and sequencing are correct. LightGuide’s system verifies the selection against the kitting list, providing immediate feedback and preventing errors from progressing unnoticed.
LEARN MORE: Augmented Reality Solutions for Part Picking & Kitting
Eliminating Assembly Errors for Complex, High-Variation Processes
The automotive industry is constantly pushing boundaries, introducing increasingly complex vehicles with intricate assemblies and high variation in component configurations. Ensuring consistent quality across multiple configurations and complex processes can be challenging, leading to rework and scrap. LightGuide’s AR work instructions offer a revolutionary approach to tackling these challenges and eliminating assembly errors in complex, high-variation processes:
- Real-time, visual guidance: Visual, step-by-step instructions are projected directly onto the work surface to guide operators through complex assemblies in real-time, eliminating the need for workers to search through manuals or decipher complex diagrams,
- Defect detection and prevention: By combining real-time guidance with 3D sensors and vision cameras, LightGuide’s AR solution creates a “no-fault forward” approach to quality control to minimize rework and ensure every component meets quality standards.
For example, LightGuide’s AR work instructions can guide multiple workers simultaneously on different tasks within the same assembly process, verifying part placement and providing feedback on pacing for each step. It can also adjust to the movement of automated guided vehicles (AGVs) and tables, ensuring instructions are always in clear view.
By offering a standardized, error-proof, and adaptable approach to complex assembly tasks, LightGuide’s AR work instructions empower automotive manufacturers to meet the demands of a changing industry, enhancing quality, productivity, and overall efficiency.
LEARN MORE: Augmented Reality Solutions for Assembly
Integrating AR with Factory Automation Systems for Improved Quality and Efficiency
The best AR solutions for automotive manufacturing tie into your MES, PLCs, and other factory automation devices, such as machine vision and 3D sensors.
To ensure the right part is built at the right time, AR from LightGuide integrates seamlessly with your automation infrastructure to receive signals directly from the operations schedule to load the correct program for the next assembly.
AR software from LightGuide also integrates with smart tools, such as digital torque guns. Through this connection, the software receives data from digital torque guns to ensure bolts are tightened in the right sequence using the correct torque. If an operator makes a mistake, the program does not allow the worker to move forward to the next step until the proper torque is applied.
Here, LightGuide is integrated with KUKA’s LBR iisy cobot to combine the benefits of industrial automation and digital work instructions to streamline the process of assembling an electrical component.
Challenge #4: Product Traceability
Traceability, also known as product traceability, is the capability to find and verify the complete history of production parts. Everything from the moment an employee scans in to start their shift to the product arriving in receiving can be tracked, analyzed, and reported.
It stands out in sectors with high quality and liability standards, but traceability is becoming equally important to quality and continuous improvement across every manufacturing industry—including automotive manufacturing. Builds are becoming more complex, yet manual production processes struggle to keep pace with rapid industry change — making them prone to error, difficult to scale, and hard to trace.
How AR Enhances Traceability in Automotive Manufacturing
Sometimes, quality problems are hard to identify. To identify the source of quality issues, LightGuide’s AR platform provides additional traceability benefits by capturing vital data, like operator IDs, serial numbers, and timestamps, throughout the production process for a detailed component record. This data can then be used to pinpoint the source of quality problems caused by a batch of raw materials, a faulty machine, a design defect, or other issues
It can also enable manufacturers to review manual process data and find opportunities for more efficiency at the individual, factory, or enterprise level. This data can be compiled into reports and dashboards—using LightGuide’s integrated Live Data Viewer or a third-party dashboarding system like Microsoft’s Power BI Platform—to paint a more complete picture of any process and the individual components that pass through it.
LEARN MORE: The Power of Product Traceability in Manufacturing
Real-World Use Cases and Success Stories
Numerous case studies prove the benefits of AR for manufacturing. Let’s explore several examples to see how AR work instructions can optimize manual manufacturing processes by empowering workers with real-time guidance.
EV Company Adopts AR for Efficient Training and Assembly
Using AR work instructions, this EV leader optimized training and assembly workflows to achieve breakthroughs in quality and productivity, including a 50% decrease in cycle time and a 75% decrease in training time.
Transmission Company Reduces Cycle Time and Improves Quality
After implementing LightGuide on a production line with four workstations and nearly 100 parts bins, this transmission supplier eliminated process confusion, reducing cycle time dramatically and improving quality by 100%.
Hydraulic Manufacturer Achieves Zero Defects With AR
Using AR work instructions, this manufacturer reduced errors in hydraulic hose systems from 769 defect parts per million to zero, saving OEMs millions in FTC calculations for final assembly.
Aerospace Leader Eliminates Defects on High-Variation Line
Global aerospace and defense manufacturer, L3Harris Technologies, must ensure its products adhere to the highest standards of quality and reliability. After implementing LightGuide’s projected AR work instructions on a line with 17 variants, the company eliminated assembly-related defects and changeover per variant.
Manage the Challenges of Automotive Manufacturing with Confidence
The future of automotive manufacturing isn’t only about automation. It’s about empowering the workforce with the best digital tools. As the automotive industry continues to evolve, are your processes agile enough to keep pace with market demands?
While the human touch is still important for manufacturers, manual processes for assembly, kitting, and inspection are inherently prone to error. And when training is inconsistent and work processes aren’t standardized, errors can multiply and amplify.
Augmented reality has already proven to be effective in standardizing manual processes and delivering consistent, effective training for leading automotive manufacturers around the world—with six of the top global automotive OEMs using LightGuide to drive operational improvement.
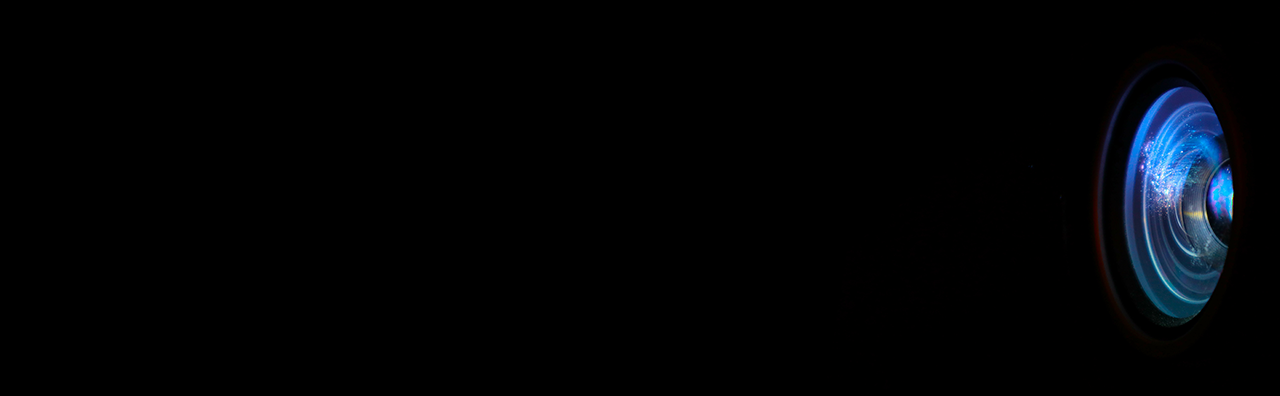
Ready to Explore How Projected AR Work Instructions Can Give Your Workforce a Competitive Advantage?
Connect with our team to see how the LightGuide platform can transform your operations.